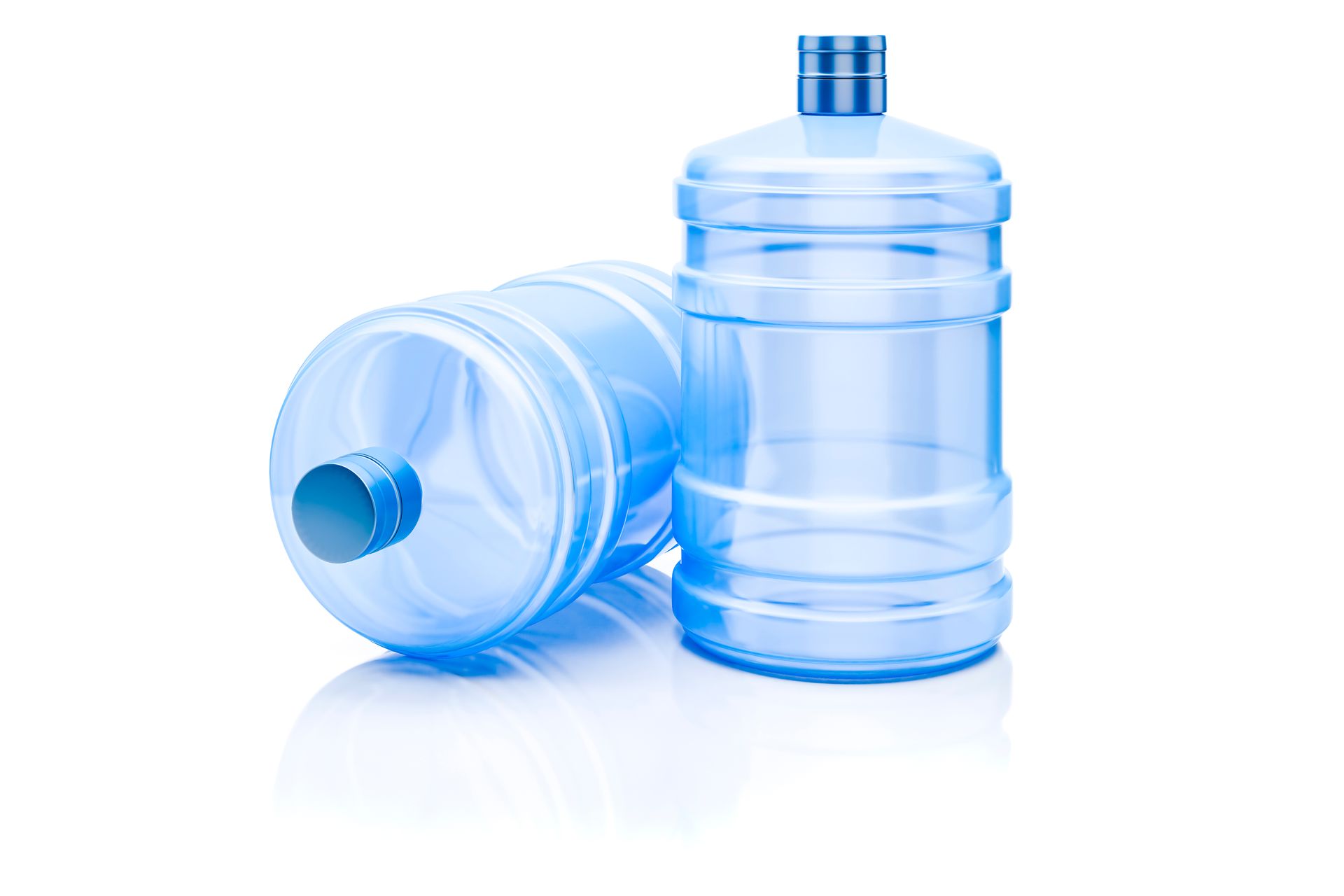
Bottled Drinking Water Quality Management
This system was developed and installed by Orasys ID at the Coca Cola 3E plant located in Aigio. The issue was to identify the 5 gallon water bottles so that the number of times each bottle is reused can be checked. In this way, the company does not allow a bottle to be reused more times than allowed and thus better ensures the quality of 3E products.
Orasys ID designed and implemented an integrated system that included the registration and placement of RFID tags on the bottles, the topology and installation of RFID readers in the bottling line, the installation of an automatic mechanism for the disposal of old bottles, as well as the middleware on which the operation of the system is based.
The equipment used was from ALIEN TECHNOLOGY. The RFID tags were GEN 2, UHF 860-960 MHz. When the bottle is first processed, the maximum allowable reuse number and the number already used (i. e. 1) are written on the tag with the corresponding dates and times. This code is also stored in the company’s computer system so that the information can be read by the computer system to extract statistics on the movement of the fleet of bottles.
As the bottles approach the gate of the antennas, a piston is activated and allows one bottle at a time to enter the reader’s field. The RFID tag is read and if the bottle is deemed suitable, it continues on its way for cleaning and filling. In case the bottle has exceeded the maximum allowed number, the system activates the automatic rejection mechanism and a pneumatic piston removes the unsuitable bottle from the aisle. In both cases, the passage of the bottle through the reader’s field of view also triggers a light alarm.
The software designed and developed by Orasys ID consisted of two parts:
-
- RFID MANAGER, which coordinates the communication of the RFID tags with the RFID reader and the peripheral control systems,
- and the bottle management application, which is responsible for counting the bottles and updating the system in real time.
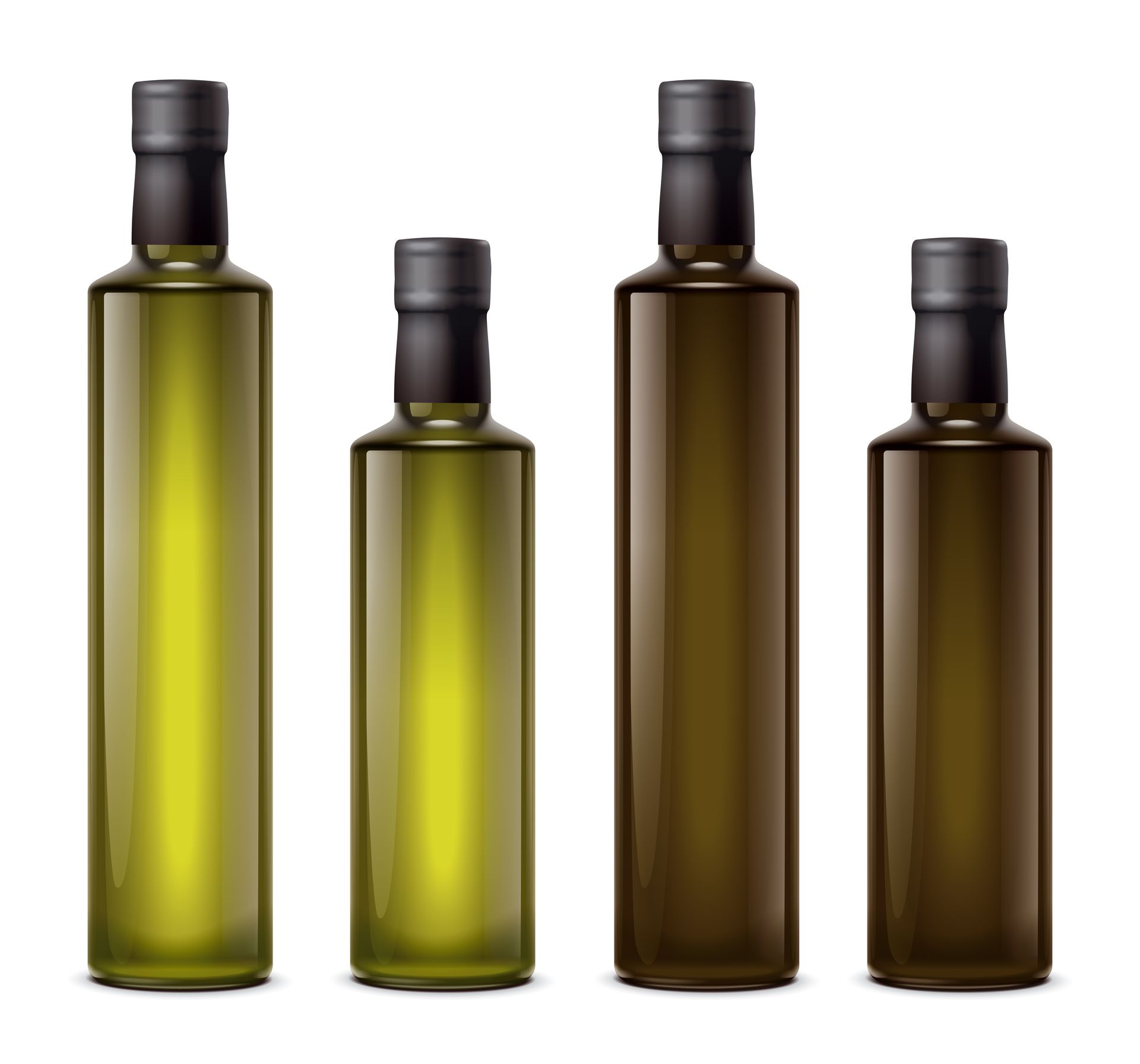
Identification and Traceability of Olive Oil
EDOEE (National Inter-professional Organization of Olive Oil and Olives) represents in Greece the main operators in the production, processing, processing, standardization and marketing of olive and olive oil products in the country and its purpose is to undertake, institutionalize measures and implement actions to strengthen the Olive Sector.
The project was the traceability and authentication of olive oil, so that the consumer can be informed about the origin and the specific characteristics of each package of olive oil and to ensure that the olive oil is genuine with an authentic label marking the package.
Orasys ID designed for the needs of this project an integrated solution that includes the marking of each olive oil package with an RFID tag carrying coded information, the provision of reading equipment (connected to a self check-in station and touch screen) and printing, as well as the development of software and its interface with the central information system of EDOEE.
The information written on the RFID tag, via printer/RFID encoder is protected by password, so that it cannot be tampered with or deleted.
By approaching the packaging at a self check-in station with a touch screen, the consumer has the ability to certify the authenticity of the packaging and at the same time, be informed of the specific characteristics of the olive oil contained in it.
The two-way transfer of data between the stations and the information system of the EDOEE, the printing and registration of RFID tags, the management of the printer (Printer /RFID Encoder) as well as the remote management of RFID readers and self check-in stations are performed by the management software (Middleware) of Orasys ID .
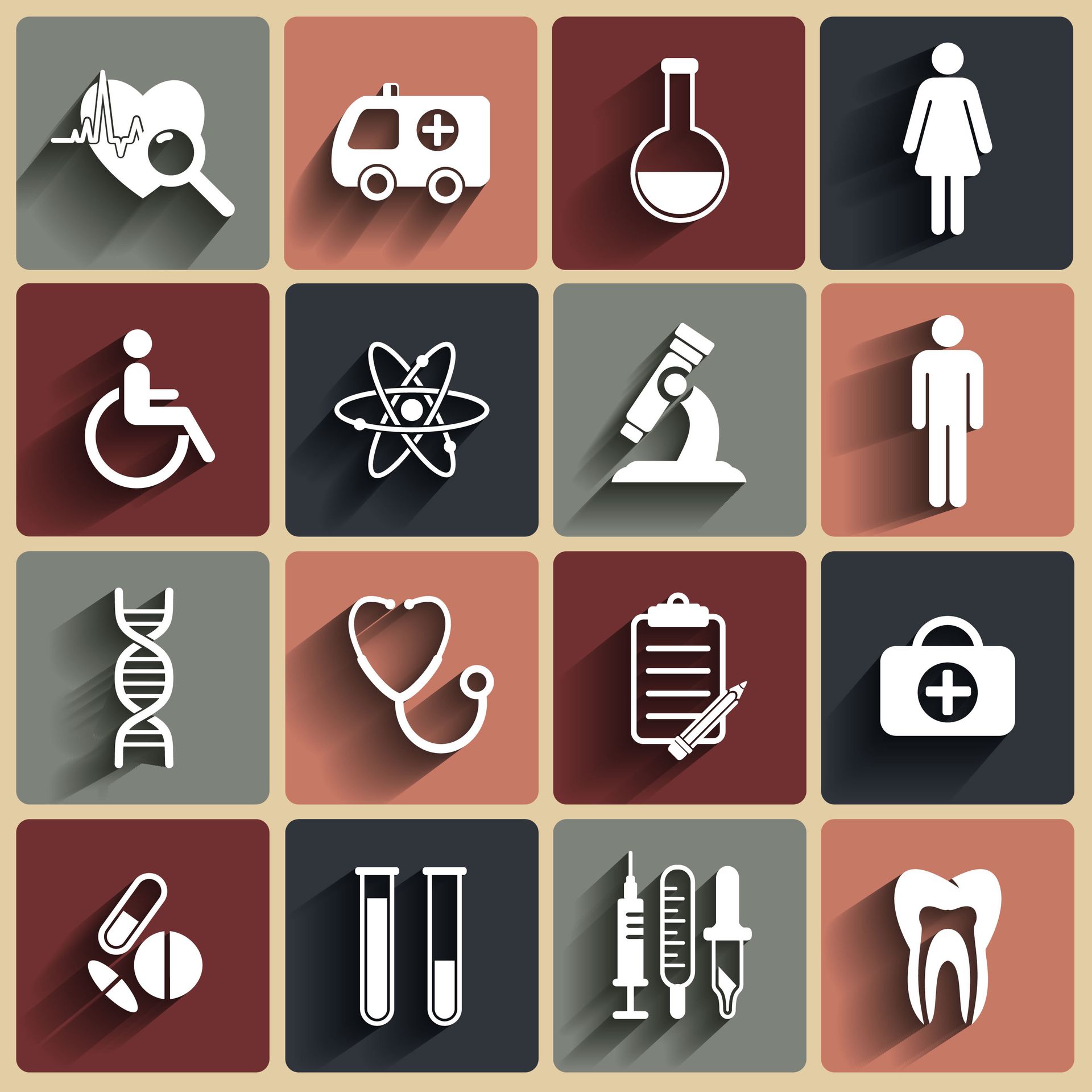
Medical Material Management
Igiasi S.A. is distributor of high quality medical devices supplying Greek Physicians and Hospitals and to fully cover their needs in fields, such as Interventional Radiology, Vascular Surgery, Interventional Neuroradiology – Neurosurgery, Interventional Cardiology – Cardiac Surgery
The operational need was for a quick and accurate inventory of medical supplies that would enable the company to monitor its stock levels and current stock levels and thus to price and replenish its medical supplies to the hospitals it supplies in a timely manner.
Orasys ID designed and implemented a solution that met the business needs of Igiasi S.A. and the way that warehouse inventory was performed (on line with WiFi), the pre-sorting, the inventory of the stock, as well as the identification and recording of expiring products.
The Orasys ID application enables the company’s warehouses to take inventory in real time via WiFi, as well as control of the shipments (pre-selection) to the customers of YGIASIASI S. A. . The operator selects a preference number and then scans the products to be shipped. By selecting the corresponding function on the terminal, the codes that read are sent via WiFi to the central system, a check is made, and the operator is informed with a message whether or not the readings agree with the order data.
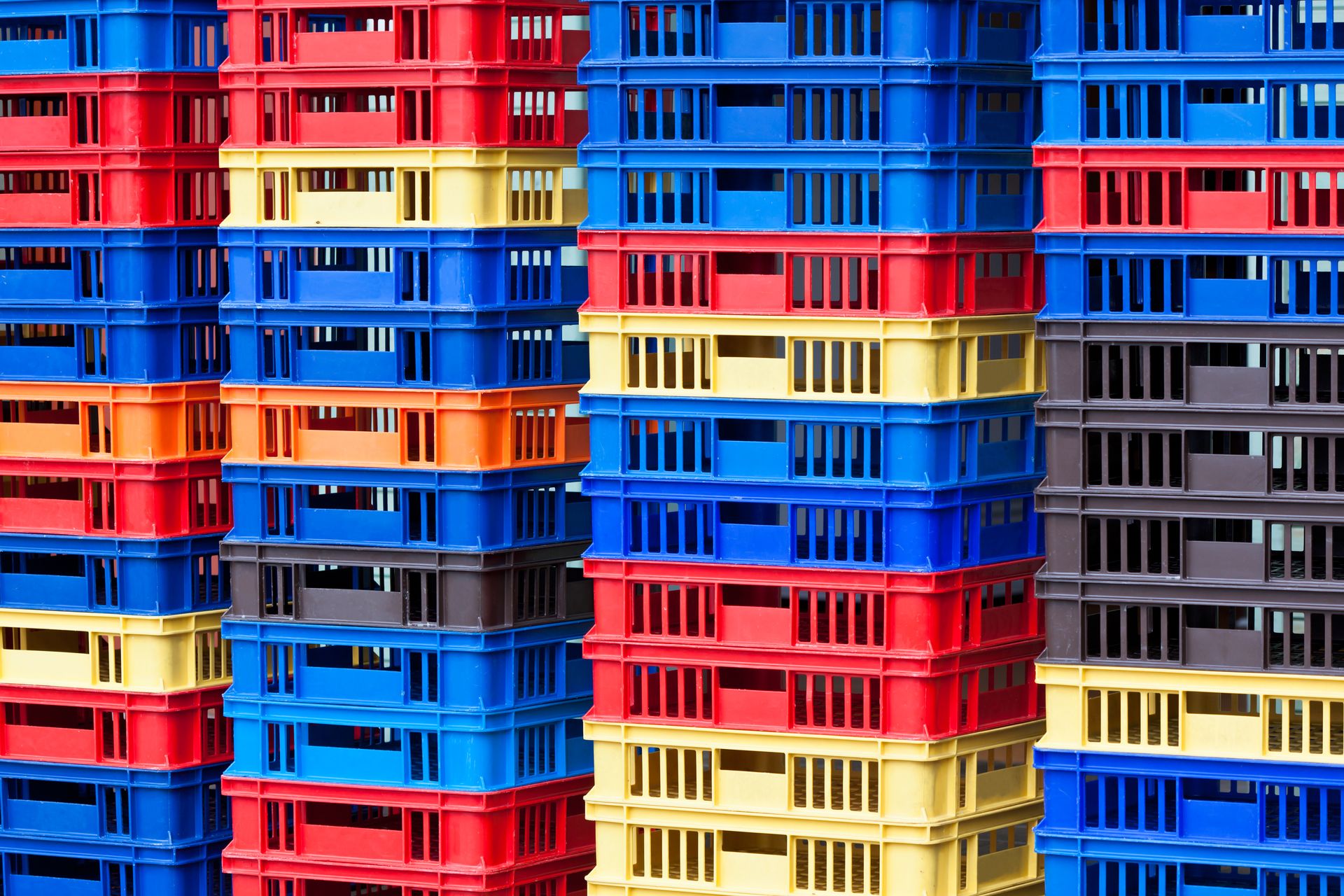
Assets Management
Coca-Cola 3E use several thousand plastic crates to transport glass bottles of soft drinks throughout Greece. These crates are considered assets and are subject to appropriate cleaning and inspection treatments at the two soft drink bottling plants.
In the context of the implementation of this project, Orasys ID developed an application for the complete management of the boxes. Specifically, for each pass of the box from the factory, the system is automatically informed by the RFID Reader about the current status of the box. The information includes the unique code of the box together with details of each processing (date, number of passes, supplier, type, destruction, etc. ). This system is accompanied by a series of management and statistical printouts.
The RFID Middleware software offered a number of features:
- Online support of all functions (production, storage, export, etc. )
- Remote management of readers
- Fine tuning – test controls, configuration
- Creation of filters for the various events
- Two-way data transfer – commands between the system and the readers
- Management of peripheral electronic devices (such as photocells, light stacks, etc. )
- Management of portable terminals.
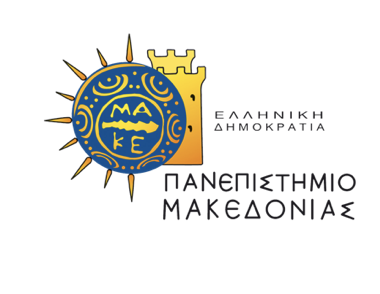
RFID tags and Library Management systems
This project was developed for the needs of the library of the University of Macedonia in order to achieve the control and the continuous inventory of books.
Orasys ID supplied and encoded all the RFID tags in order to meet the project’s requirements, such as the smooth operation of a modern library, the increasing volume of borrowed and returned books, reduction of time needed for inventory process.
The ability to identify a book, without the librarian or machine making eye contact with it, practically means that the process of borrowing or returning a book can be done simultaneously for several books, by simply moving them in front of an RFID reader. The advantage of this method is that the system is updated in real time, quickly and reliably, compared to bar code technology, which requires identification separately for each book (one at a time, targeting a specific part of the book).
The ability to locate and recognize the RFID tag remotely simplifies and speeds up the inventory process in a library: the inventory that would require a lot of time, staff commitment and possibly the closure of a section or even the entire library, can now be carried out in a minimum of time, without hindering the service of the library users.
Also, the lack of contact with the books protects them from damage caused by clumsy handling, but at the same time simplifies a very tedious, laborious and monotonous process for the staff.
RFID tags have a longer lifespan than existing library management systems, and therefore offer greater long-term reliability.
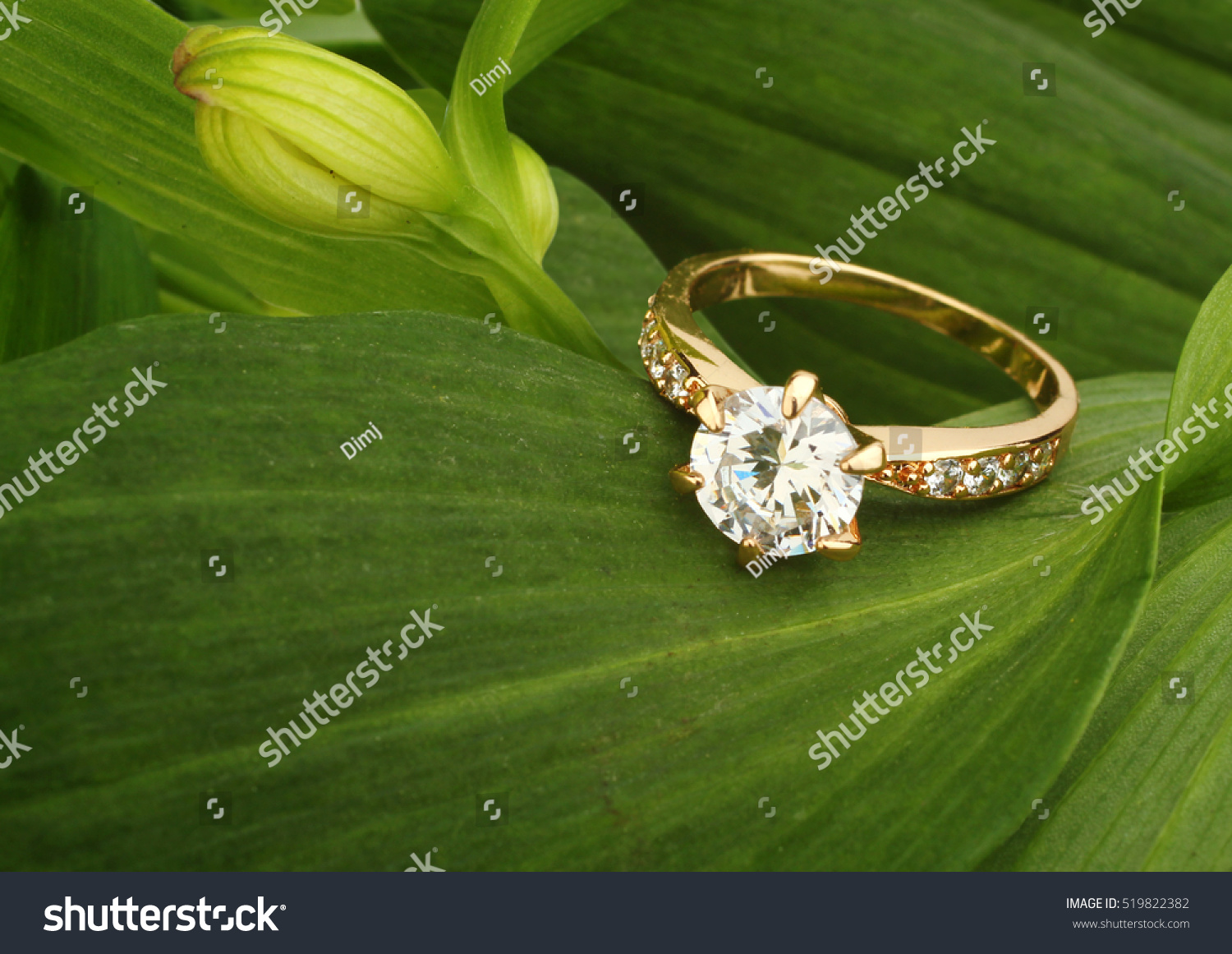
Jewellery Management
This project was developed for the management (distribution, inventory) of jewellery. It is worth noting that RFID technology is particularly useful in the management of high-value materials.
The solution that was developed by Orasys ID based on RIFD technology, installed and is currently operational, covering four main areas:
- Jellewery delivery
- Selling process
- Inventory process
- Detecting Jewellery in Wrong Position
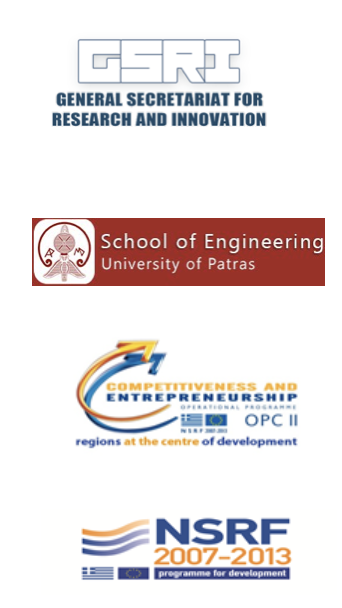
Document Management System using Radio Frequency Identification Technology – “SELIDA”
Pilot project for the development of an integrated and innovative system for the management of printed material, which will be based on Radio Frequency Identification (RFID) technology, its efficient interconnection with Back Office systems and the use of web services (Object Naming Service – ONS) for the dissemination of information that characterizes each printed material.
The project implemented at the “Library & Information Centre of the University of Patras”, capturing all the knowledge that will result from the individual actions of the project.
Critical documents, legal and financial documents, rare and/or high value books can be managed using an RFID tag so that it can be tracked at any time at various levels (location, time, owner, etc. ), allowing printed books to inherit a digital identity and enabling information systems, whether they are resource management (ERP, WMS, etc. ), process management (WorkFlow, Document Management, etc. ) or special purpose (Library Management Systems), to identify and manage them.
Searching and managing them through information systems will be as easy as searching for information through web applications.
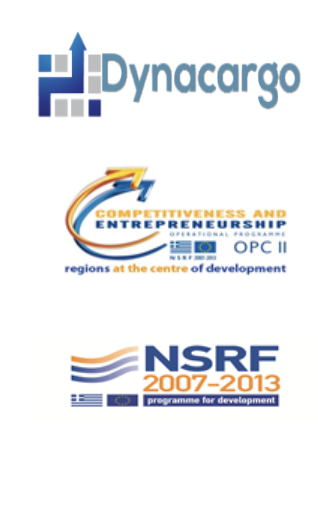
Dynamic Cargo Routing on-the-go
The “Dynacargo” pilot project aimed to develop a flexible waste collection vehicle fleet management system with improvements based on the load in the bin, in order:
- Reduce human errors
- Free vehicle drivers from load management
- Optimize vehicle and staff utilization
- Reduce emissions and vehicle-related costs (fuel, maintenance, etc.).
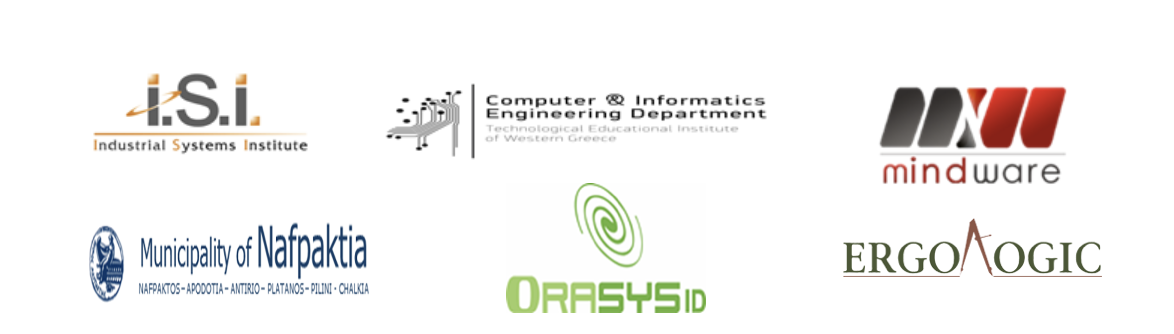